Optimizing Assembly Production with Non-Synchronous Pallet Conveyors
Posted on
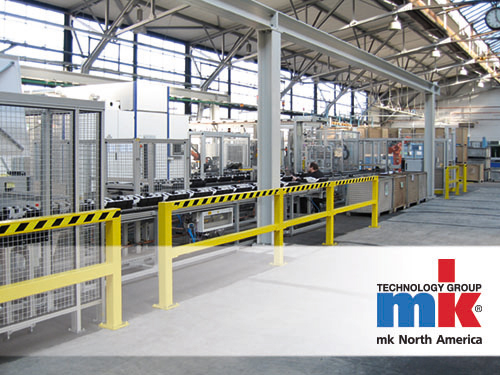
Staying competitive in manufacturing is a difficult task these days. Costs are rising and margins are narrowing, all while demands for innovation in research and development increases across industries.
While some of the challenges inherent to modern manufacturing simply have to be lived with, there are some areas where manufacturers have a great deal of control. Among the most significant is in optimizing assembly production.
When one factors in labor, time, and other resources, assembly accounts for as much as three-quarters of total manufacturing costs for any given product. By making sure assembly production is optimized, manufacturers can make considerable gains in improving overall efficiency and lowering costs. But as with most things, this can be easier said than done.
Challenges in Optimizing Assembly Processes
While every facility is different and every product has different manufacturing requirements with their own unique demands, there are some pain points that are more or less consistent across many modern manufacturing operations. These can include the following:
- Increasing product complexity: As the number of components increases and assembly becomes more sophisticated, product staging must become more complex. This makes simple, straight assembly lines insufficient.
- Mixing of automated and manual assembly processes: Complex assemblies might mean that modern robotic integrations aren’t yet up the task of full automation. This can sometimes necessitate manual assembly stations in between automated processes. Creating a single consistent assembly line to meet this necessity can pose a serious challenge.
- Multiple products assembled on a single line: When one product is phased out and another introduced, it is often cost-prohibitive to completely rebuild assembly infrastructure. It is therefore necessary to have production lines with the flexibility to accommodate a broad variety of products. Likewise, streamlining the assembly process across multiple parallel product lines might necessitate using a single, versatile assembly line.
- Specialty environment requirements: Harsh environments, high temperatures, clean rooms, and other specialty environments can all pose further challenges external to the production line itself, requiring specialized solutions.
How Modular, Asynchronous Pallet Conveyors Can Meet the Needs of Manufacturers
An ideal solution to many of these challenges is the use of asynchronous conveyor systems, which can provide independent movement between different staging areas. This provides maximum flexibility, allowing for continuous flow of certain products and components while others are independently routed to more time-consuming or sensitive staging areas.
The use of workpiece pallets on an asynchronous line allows for further precision in staging, accumulation, and timing applications. This is especially true with modern computerized controls and programmable logic computers (PLCs).
mk North America’s VersaMove line of non-synchronous pallet conveyor systems is an example of a robust assembly solution for modern manufacturers. Offered in three platforms, VersaMove Standard, VersaMove Plus, and VersaMove Ultra, for maximum versatility, mk’s pallet conveyor systems offer the flexibility to handle assembly operations in industries as diverse as automotive, computers, and consumer goods.
Modular design means that new lines can be integrated and reused as needed with options to customize workflow, improve worker ergonomics, and reduce system footprint according to each manufacturer’s specific requirements.
To learn more about how the VersaMove and other conveyor systems from mk North America can help to optimize your assembly processes, get in touch by calling (860) 769-5500 or by using the form below.